SAVING FUEL, MONEY AND THE ENVIRONMENT
The consequences of reducing fuel usage and our carbon footprint in the transport industry will be considerable and far-reaching. As part of the global transport sector, a recognized major source of pollution , our industry is coming under increasing pressure to make a greater contribution to a carbon-zero future. Thankfully, these issues are finally getting the world’s attention and, at Aerodyne Global, we are ready to help you achieve immediate savings with our easy-to-use solutions.
WHY FOCUS ON TRUCK AERODYNAMICS?
Making your fleet more aerodynamic means reducing drag and improving flow control. Drag is the resistance of the vehicle as it moves through the air – it will be determined by the shape of the truck, hence why adding our devices reduces this. Doing so has a guaranteed impact on emissions without reducing your efficiency or requiring wholesale change to your vehicles.
Flow control is all to do with how steady your ride is. It refers to the ease with which the vehicle moves, or flows.
The Technical Explanation
The overall shape of a vehicle is measured as the Coefficient of Drag, (Cᴅ). By enhancing the aerodynamic shape of a truck and therefore reducing the drag resistance, improves the flow control around the vehicle. Drag reduction devices do this, saving engine power and therefore fuel whilst give the vehicle a steadier ride.
Typical Cᴅ figures in the automotive world are as follows:
Vehicle Type | Typical Cᴅ |
Best in class production car | 0.22 + |
HGV without Truck Aerodynamic Devices | 0.7 – 0.9 |
HGV with Truck Aerodynamic Devices | 0.6 – 0.7 |
Adding aerodynamic devices will reduce the Cᴅ, and this is typically measured in counts, (1 count = 0.001 Cᴅ). In the car world, aerodynamicist’s will look seriously at improvements with 1 or 2 counts, this could be a result of very small detail e.g. the wheel or tyre design. In comparison, well designed HGV aerodynamic devices can reduce the Cᴅ by 10 – 20 counts, providing a significant improvement.
Types of truck aerodynamic devices
There are many types of truck aerodynamic devices available, below you will find the most common ones.
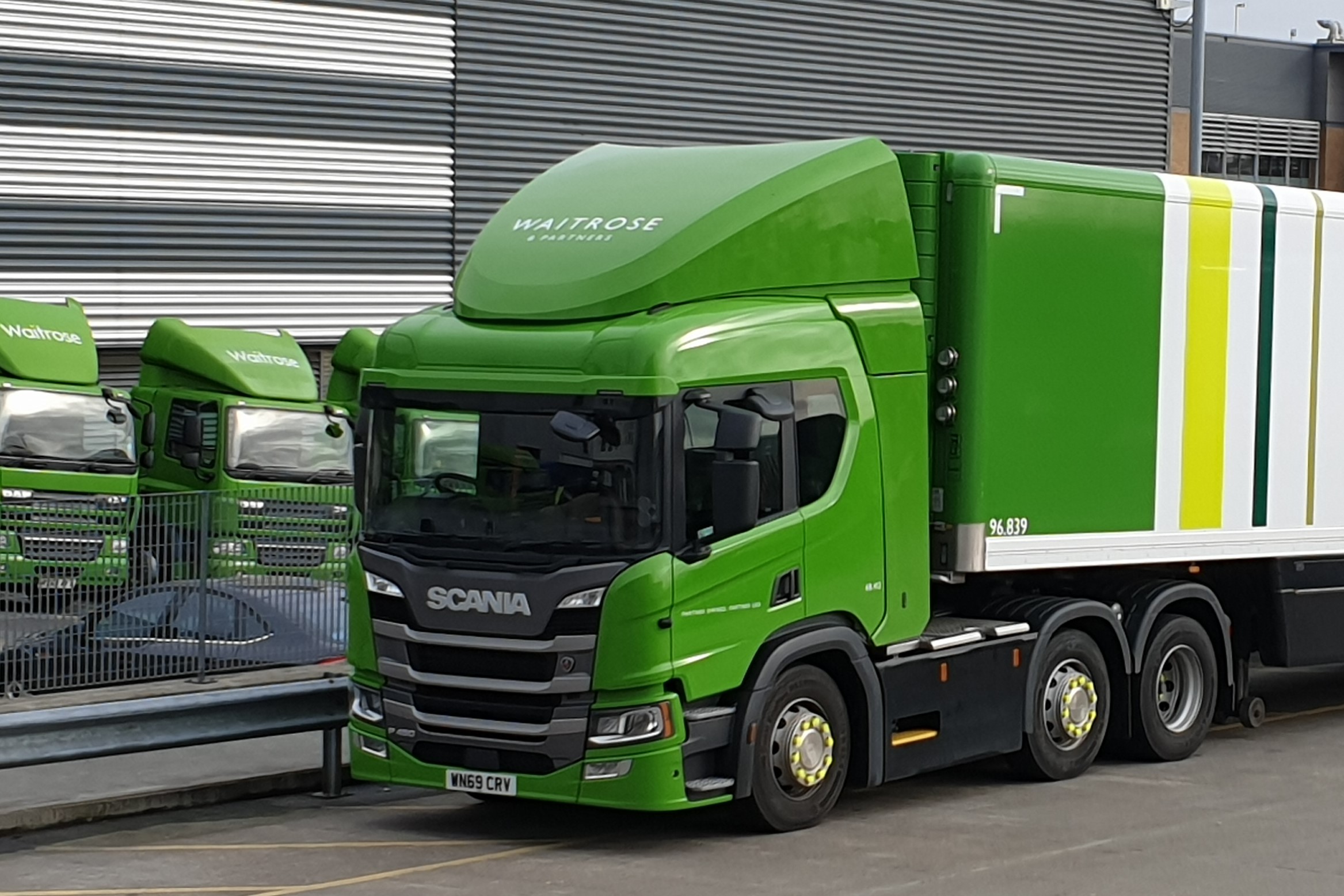
Fitted to top of cab
This helps the flow control from the front of the cab and lifts it up over the body or trailer. Available in fixed or adjustable height options.
This is essential for tractors pulling trailers with an overall height higher than 4m (13.12ft). Factory air management kits only optimise airflow for the standard 4m European trailer.
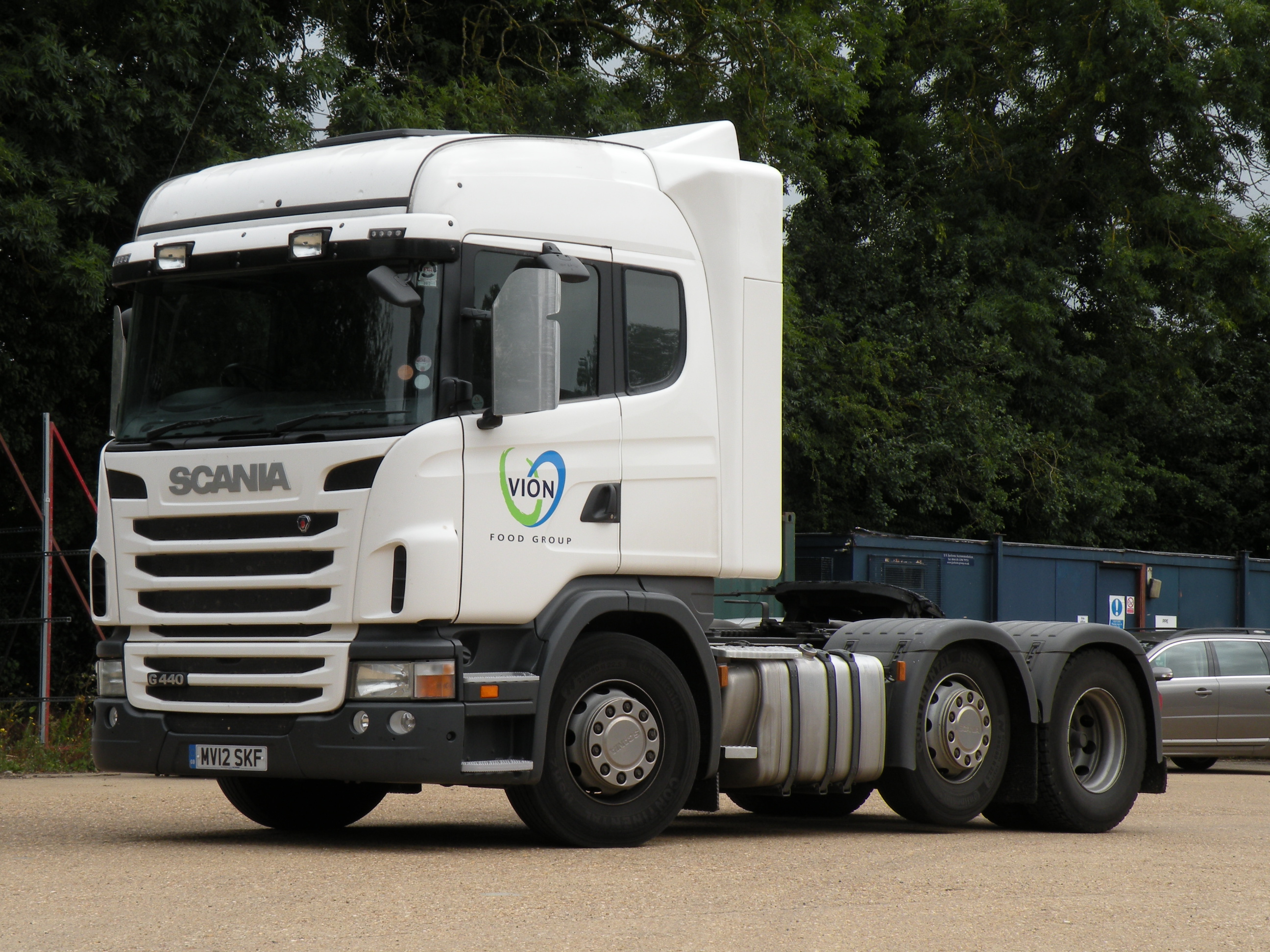
Fitted to rear vertical corners of cab
These help push the air out around the width of the body as well as fill in the cab to body gap which is particularly effective when the vehicle is in a yaw.
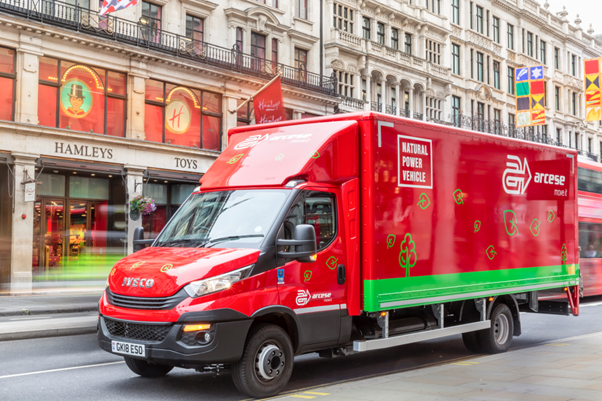
THE COMBINATION OF A CAB TOP DEFLECTOR AND CAB REAR SIDEWINGS (RECOMMENDED)
Otherwise known as a FULL KIT, AIR MANAGEMENT KIT OR AMK. This solution gives the ultimate cab to body / trailer front aerodynamics.
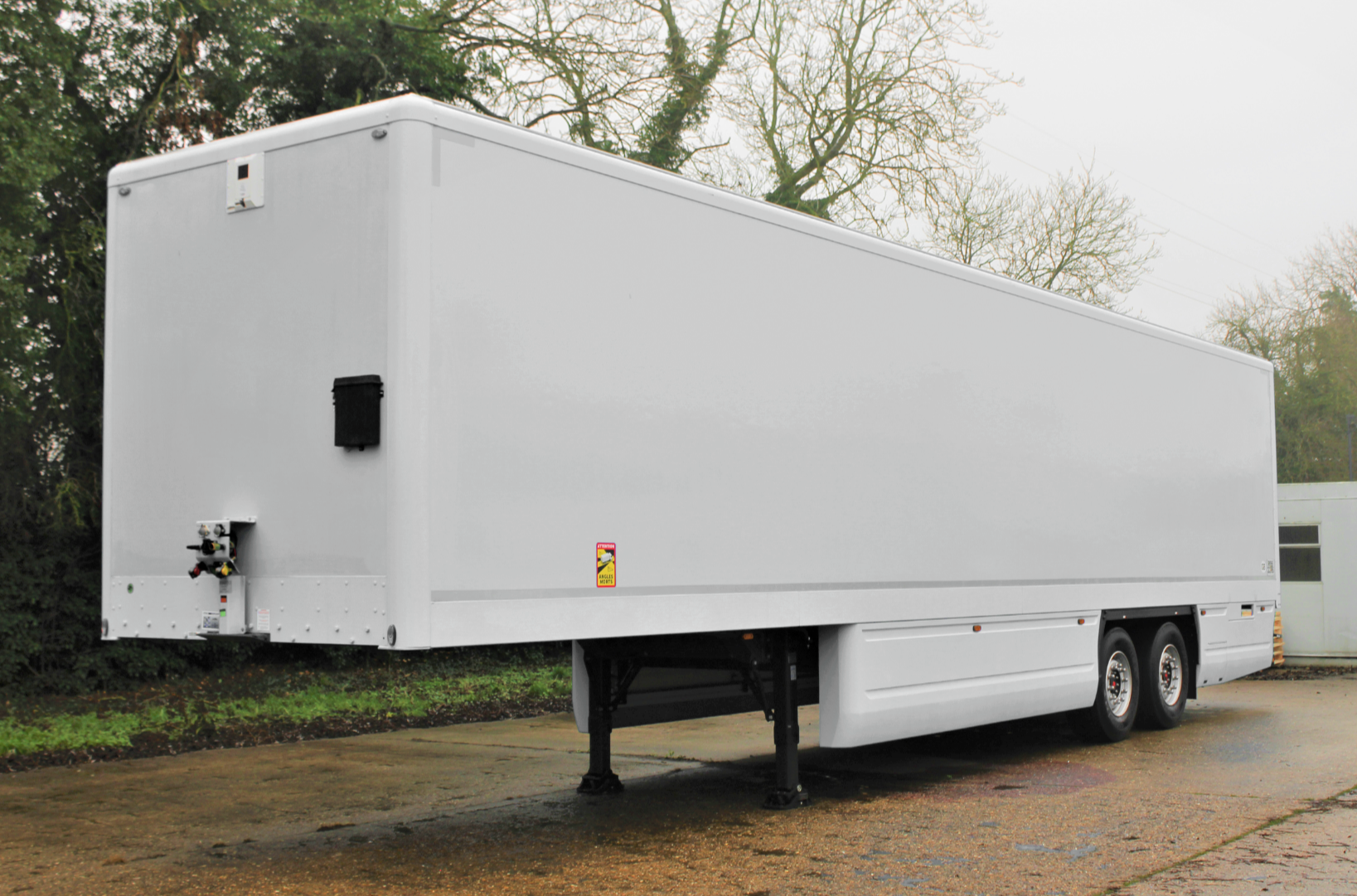
Fitted under the body / trailer and between the wheels on a tractive unit
Whilst also giving great styling they prevent drag under the vehicle / chassis and keep the flow control regular as it travels rearwards from the cab.
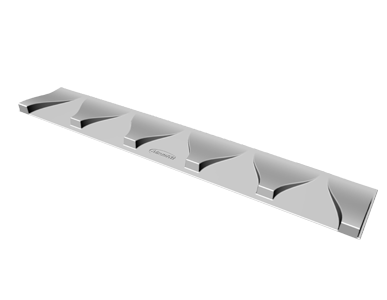
Normally fitted at the rear of the body / trailer roof
These aerodynamic devices, consist of a small vane usually attached to a lifting surface at the rear of the vehicle and modify the boundary layer, creating less air drag as it leaves the rear of the vehicle.
What forces impede motion?
Assuming a steady speed on a level road, the truck needs fuel to overcome the following forces:
Drivetrain Friction
Tyre Rolling Resistance
Aerodynamics Drag
Drive train friction is usually the weakest force consuming only about 15% of the engine power. Tyre rolling resistance (what you feel when you push a car from stand still) consumes power proportional to road speed. So double your speed and you need twice the power to push the vehicle along. The real shocker is aerodynamic drag (what you feel with your hand out of a car window at speed), requiring minimal power at low speeds it rises exponentially as the vehicle increases speed. The power required to overcome it is proportional to the cube of the speed (v³). Aerodynamic drag is the quickest and easiest force to counteract and will have the greatest impact once Aerodyne products have been fitted to your fleet. Because we can retrofit products to older vehicles, you don’t need to review your fleet. Browse our range of products and start reducing your carbon footprint immediately.
For example… Double the speed and you need eight times the engine power to overcome the air drag. In this context, the heavy demand on engine power to overcome air drag means a rapid usage of fuel at high speeds.
The concept of drag - dominant speed (DDS)
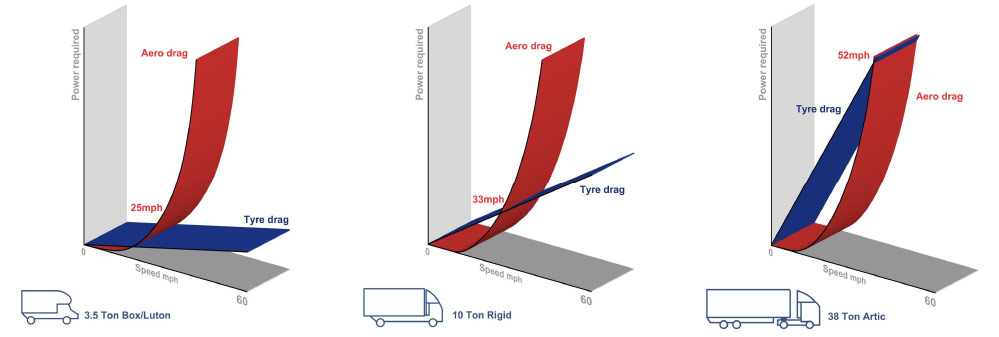
The graph here shows that as speed rises air drag eventually takes over from tyre rolling resistance to become the chief fuel consuming force. This point is called the ‘Drag-Dominant Speed’. Aerodynamic drag has become very significant by the time we reach this speed, and as speed rises further, the effects of drag on fuel consumption will be dramatic. The graphs also demonstrate that good fuel savings can therefore be made at surprisingly low speeds on light and medium trucks (e.g. 20-35 MPH and above). You don’t have to be trunking on the motorway with such vehicles to save fuel.
Explore our product range